Rozhovory
Investice do technologií obrábění jako cesta k udržitelnosti
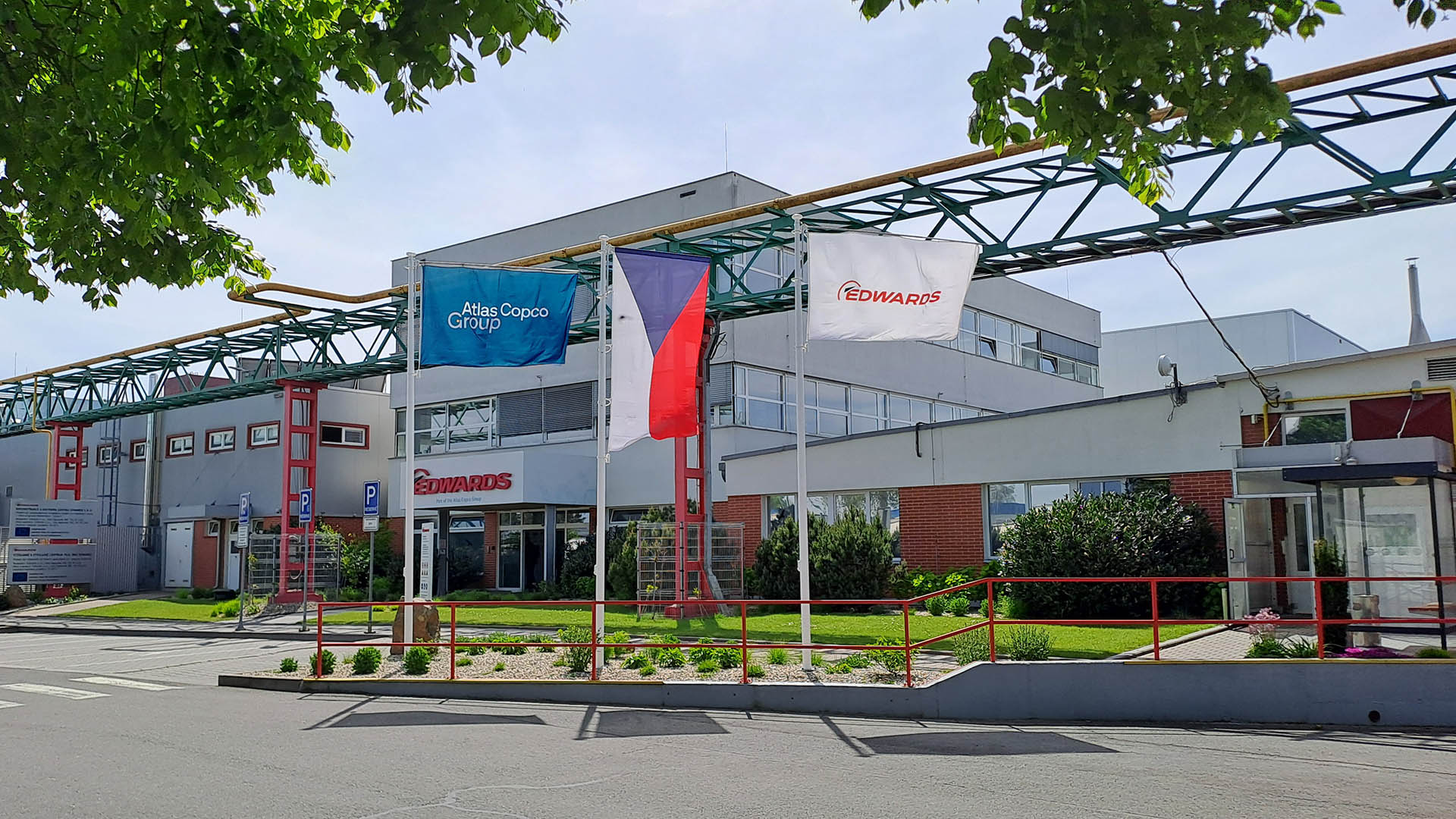
Výrobní závod firmy Edwards v Lutíně u Olomouce, foto: Edwards, s.r.o.
Společnost Edwards, s.r.o., ve svém výrobním závodě v Lutíně u Olomouce vyvíjí a vyrábí špičkové vědecké i průmyslové vakuové vývěvy. Je součástí britského koncernu Edwards Ltd, který je od roku 2014 dceřinou společností švédské skupiny Atlas Copco Group. Lutínský Edwards patří k významným zaměstnavatelům olomouckého regionu a svou pozici nadále posiluje. Kvalita vyráběných vakuových vývěv je pro firmu Edwards zásadní, proto si klíčové komponenty obrábí vlastními silami a investuje do nových technologií obrábění. O investicích do modernizace strojového parku a jejich dopadech na produktivitu a efektivitu výroby jsme hovořili s Martinem Filipovičem, který se svým týmem zavádí v Edwards nové obráběné díly do výroby.
V letošním druhém čísle Reportáží z průmyslu jsme v rozhovoru s generálním ředitelem lutínského výrobního závodu Edwards Janem Večeřou hovořili o plánovaných investicích na letošní rok ve výši 300 milionů korun. Jak do vašich investičních plánů zapadají výdaje na obnovu strojového parku?
Investice do obnovy strojového parku hrají v investiční strategii klíčovou roli. V současné době je v našem závodě umístěno přes 80 obráběcích center, na kterých obrábíme komponenty pro naše vakuové vývěvy. Jejich inovace vyžadují, abychom neustále posouvali hranice přesnosti obráběných komponent, protože i nejmenší odchylky mohou mít vliv na funkčnost a spolehlivost našich finálních produktů.
Investice do obnovy strojového parku jsou pro nás důležité také proto, že přinášejí významné snížení provozních nákladů a zároveň podporují udržitelnost našeho provozu. Nové stroje spotřebovávají méně energie, jsou spolehlivější a nevykazují tak vysoké náklady na údržbu jako původní stroje. Nové technologie také přispívají k dosažení našich cílů udržitelnosti, protože jsou energeticky úspornější a pomáhají nám snižovat naši uhlíkovou stopu a množství produkovaných odpadů.
Jaký konkrétní investiční projekt v této oblasti v letošním roce realizujete?
V letošním roce jsme rozhodli nahradit tři stávající obráběcí stroje značky Stama, což představuje investici vyšších desítek milionů korun. Zásadním kritériem pro rozhodování o směřování naší investice bylo stáří našich současných strojů. Dva z nahrazovaných strojů jsou již na hranici své životnosti a nesplňují parametry, které od moderního obráběcího procesu očekáváme.
Připravili jsme tedy investiční projekt na nákup nových strojů Stama a investici obhájili na úrovni vedení divize vakuové techniky naší mateřské společnosti Atlas Copco Group. Celý proces přípravy však zabral nějaký čas, a než jsme stihli vystavit objednávku na nové stroje, zjistili jsme, že jejich výroba byla ukončena a byli jsme nuceni hledat alternativu.
Jaké alternativy jste zvažovali a jak jste postupovali při výběru nového stroje?
Zásadním kritériem pro nás byla obdobná funkcionalita jako u strojů, jež potřebujeme nahradit. Hledali jsme dvouvřetenový obráběcí stroj s podobnou produktivitou jako původně zamýšlené stroje Stama. Oslovili jsme víc dodavatelů, mezi nimi i stávajícího dodavatele Stamy, firmu Chiron Group, která nám nabídla jiný stroj z jejich portfolia.
Dva potenciální stroje od různých dodavatelů jsme vybrali do dalšího testování a provedli jsme zkoušky obrobitelnosti a časové studie, abychom zjistili, za jak dlouho dokáže stroj vyrobit díl podle našeho výkresu. Kromě přijatelného času obrábění je pro nás důležité, aby byl stroj dostatečně přesný a vyráběl díly v požadované kvalitě. Proto jsme vyrobené obrobky podrobili měření nejen u dodavatele, ale přímo v našem závodě na našem měřicím zařízení.
Jaké byly výsledky těchto testů a jaký stroj jste nakonec vybrali?
Na základě testů jsme se nakonec rozhodli pro stroj od firmy Chiron. Jejich pětiosý obráběcí stroj se dvěma vřeteny je vybaven plnou automatizací a bude schopný vyrábět celé portfolio našich statorů pro RV vývěvy 24 hodin denně, sedm dní v týdnu. Součástí stroje je robotický systém se zásobníkem dílů. Operátor připraví různé typy dílů a stroj poté automaticky pokračuje v jejich obrábění dle specifického typu. Součástí celé investice je také vybavení obráběcího centra potřebnými nástroji a novým měřicím zařízením. Dodání stroje očekáváme v listopadu a uvedení do plného provozu začátkem příštího roku. Do té doby musíme připravit pro nový stroj místo. Neznamená to totiž jen odstranit původní stroje, ale například také připravit podlahu pro vysoké zatížení, které nový stroj představuje.
Jaké přínosy očekáváte od této investice?
Očekáváme, že nový stroj nám umožní ušetřit padesát procent času na výrobu jednoho statoru a snížit náklady na údržbu stroje. Díky úspoře strojního času zajistíme nejen dostatečné kapacity pro naši stávající výrobu statorů RV vývěv, ale současně vytvoříme i potenciál dostatečných kapacit, abychom mohli do sériové výroby zavést novou řadu RV vývěv, na nichž pracuje náš vývojový tým.
Úspory nákladů však nejsou jediným přínosem, který od investice očekáváme. V rámci skupiny Atlas Copco Group směřujeme k naplňování cílů iniciativy Science Based Targets a ke snižování emisí uhlíkových plynů. Veškeré naše investice tedy posuzujeme i s ohledem na jejich vliv na životní prostředí a naší volbou jsou jednoznačně udržitelné technologie a energeticky efektivní zařízení. Konkrétně u této investice očekáváme roční úspory emisí CO2 přibližně 249 tun za rok, což nás významně posune k našemu cíli stát se do roku 2025 CO2 neutrálním závodem.
Investice tohoto rozsahu však v lutínském Edwards není ojedinělá, ale je součástí dlouhodobého investičního plánu rozvoje závodu. V minulém roce jste dokončili obdobnou investici do obnovy strojového parku zaměřenou na efektivitu a automatizaci obráběcího procesu. Jakých výsledků dosahujete?
Projekt, na který se ptáte, jsme zahájili již v roce 2021. Po analýze výrobního toku a uvážení vyšší efektivity nových technologií jsme přistoupili ke spojení a automatizaci několika procesů. Dva zastaralé soustruhy jsme nahradili jedním novým a zároveň jsme stroji předřadili automatický zásobník na polotovary a přímo za stroj jsme instalovali plně automatizovanou měřicí stanici, která stoprocentně kontroluje rozměry jednotlivých obrobků. Tím jsme dosáhli velmi zajímavého zefektivnění celého procesu – zredukovali jsme obráběcí čas o neuvěřitelných 73,7 procenta a nová technologie, i když nahradila dva stroje, má o 20 procent vyšší počet vyrobených kusů. Zpracovací náklady se nám již v tomto kroku podařilo snížit o 13 procent u produktu, který je z pohledu objemu výroby významný. Díky tomu jsme dosáhli velmi zajímavé návratnosti investice.
V dalším kroku jsme dokoupili pětiosé frézovací centrum a celý proces minulý rok dokončili připojením automatizace s robotem. Kromě výše uvedených přínosů nám nově instalovaná automatizace umožňuje nepřetržitou výrobu bez zásahu operátora po dobu až 24 hodin.
Budete v investicích do strojového parku dále pokračovat?
Určitě ano. Zmíněné příklady jasně ilustrují, že přínosy investice do obnovy strojového parku v podobě zvýšené produktivity, zkrácení výrobních časů, menší spotřeby zdrojů, úspory nákladů na údržbu strojového parku a minimalizace dopadů na životní prostředí vytvářejí synergický efekt, který zlepšuje naši konkurenceschopnost. Vytváří totiž předpoklady pro dlouhodobý úspěch firmy Edwards a naplnění naší vize stát se nejlepším závodem vakuové techniky, který dodává vakuové vývěvy do celého světa.