Novinky
Digitální dvojče v průmyslové praxi II
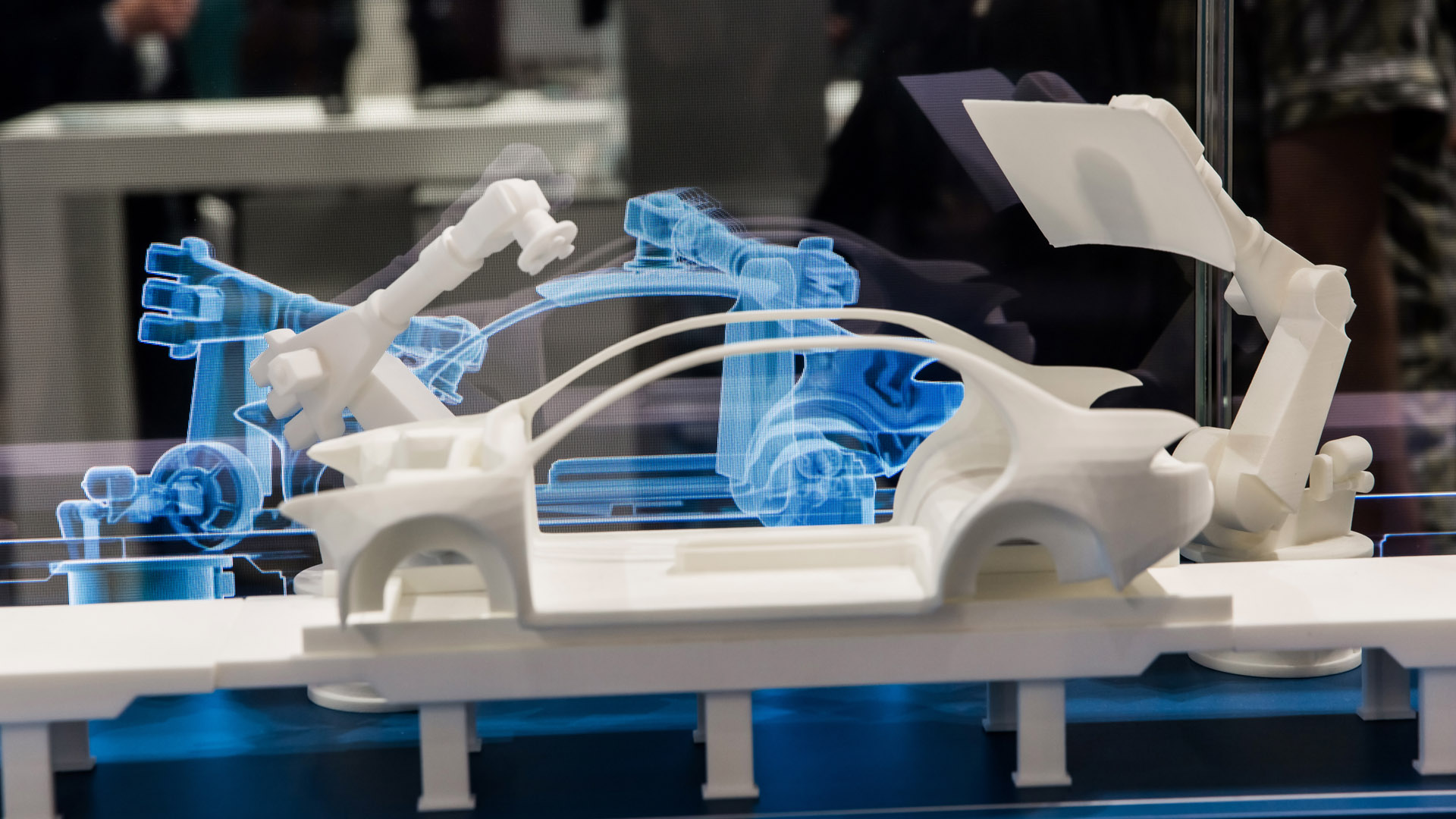
Národní centrum průmyslu 4.0, které je součástí Českého institutu informatiky, robotiky a kybernetiky ČVUT v Praze, uspořádalo letos 26. května videokonferenci s názvem Digitální dvojče v průmyslové praxi II. Akce představila na příkladech z výrobní praxe technologii, jež firmám umožňuje digitálně nasimulovat výrobky, výrobní zařízení nebo i celý výrobní proces, a tak dopředu odhalit případné chyby či úskalí plánované výroby. Časové i finanční úspory takového postupu jsou zřejmé a i přes finanční náročnost samotné technologie je její návratnost překvapivě rychlá a výhody zřetelné. Konference Digitální dvojče v průmyslové praxi I se uskutečnila loni v listopadu.
Zvýšení efektivity produkce kompresorů díky digitálnímu dvojčeti ve výrobním a montážním závodu společnosti Secop ve Zlatých Moravcích na Slovensku představil její manažer produkce František Šlosiar. Jak uvedl, jedná se o výrobní linku zčásti robotizovanou a automatizovanou, zčásti s určitým podílem lidské práce. Problém, který chtěla firma vyřešit, byla mikrozdržení, k nimž na lince docházelo mezi jednotlivými operacemi. Secop očekával, že díky digitalizaci se výkon linky zvýší o 15 procent. Takové navýšení produkce by v přijatelném čase pokrylo investiční náklady.
Digitální kopii fyzického výrobního systému, která se chová stejně jako fyzický výrobní systém a navzájem s ním komunikuje, vytvořila československá společnost Sidat Digital. Její jednatel Robin Mitana mimo jiné konstatoval, že především bylo třeba technicky sjednotit sběr dat z jednotlivých výrobních operací na lince, protože výstupy z některých snímačů nebyly navzájem kompatibilní a někde datové senzory zcela chyběly.
Operační systém, který umožnil data dále zpracovat pomocí aplikací a pokročilých analytických funkcí a proměnil je v chytrá data zvyšující efektivitu výrobní linky, vytvořila společnost Siemens. Celý projekt realizovaný ve Zlatých Moravcích v duchu průmyslu 4.0 za 12 měsíců pod vedením Františka Podzimka, ředitele divize Digital enterprise společnosti Siemens, dosáhl zvýšení výkonu linky z dvou tisíc kusů kompresorů za směnu na 2300 kusů.
Digitalizace vyžaduje změnu myšlení
O praktických zkušenostech z digitalizace průmyslových procesů mluvil Petr Musil, výkonný ředitel inženýringu společnosti Del. Kromě jiného zmínil, že úspěch řešení závisí také na technické vyspělosti zákazníka, a tedy jeho schopnostech formulovat zadání projektu a pochopit komplexní povahu výsledného řešení, které z 90 procent znamená změnu v řízení výroby. Podle Musila využití možností průmyslu 4.0 vyžaduje změnu myšlení i způsobu práce. Dodal, že velkou výhodou řešení pomocí digitálního dvojčete je vizualizace celého projektu před jeho uskutečněním. Jak řekl, virtuální kopie výrobních procesů umožňuje modelovat jejich činnost, vytvářet variantní řešení a předvídat dopady plánovaných změn na jednotlivé součásti systému i na jeho celkový výkon.
Nad výhodami zavádění digitálních technologií a nad jejich přínosem pro efektivitu firmy se zamýšlel Lukáš Jílek, seniorní manažer v poradenském oddělení strategie a provozních činností ve společnosti Deloitte Česká republika, která výrobcům radí, jak přejít na digitální způsob řízení a provozu. Jílek v této souvislosti hovořil o zlevňování elektronických zařízení, pokroku ve zpracování a interpretaci dat získaných z procesů i o nových možnostech poznání podstaty fungování technologických procesů, chování materiálů a jejich vzájemných interakcí. Na základě poznatků firmy Deloitte rovněž uvedl, že nadnárodní společnosti, které mají centrály v zahraničí, své české pobočky digitalizují až ve druhém sledu. Ve světě využívá výhod průmyslu 4.0 již 24 procent velkých firem, v České republice je to asi 13 procent. Světové firmy jsou proto asi o dva roky napřed. Podle Jílka je digitalizace nevyhnutelná pro všechny podniky, ale malé a střední firmy musí zatím pečlivě analyzovat, zda se jim taková změna, která představuje investici řádově v jednotkách milionů korun, vyplatí.
Automobily se přestěhují do virtuálního prostoru
Koordinátor konstrukčních systémů a systémů vozu z technického vývoje Škody Auto Václav Jechura vysvětlil, jak digitální dvojče využívá náš největší výrobce automobilů například z hlediska bezpečnosti, tedy pro simulaci crashtestů a podobně. Vedle toho umělou inteligencí založenou na cloudové technologii spoří Škodovka náklady spojené s logistikou. Také konfigurátor vozů Škoda již běží na digitální bázi.
Podle Jechury se podstata automobilu bude postupně stěhovat z fyzického do virtuálního světa, kde budou v cloudech shromážděna data pro autonomní řízení, která po zpracování umělou inteligencí umožní předvídat a včas reagovat na různé dopravní situace, a eliminovat tak rizika. Podobně bude sledován technický stav vozidla a za pomocí IoT bude prováděna jeho údržba. Jak Jechura dodal, přesun do kyberprostoru bude ovšem vyžadovat velmi vyspělé softwarové zabezpečení dat a informací.
Generální ředitel a spoluzakladatel společnosti Pocket Virtuality Jan Hovora představil, jak je možné využít kombinaci rozšířené reality a digitálního dvojčete k dálkově navigované údržbě, montáži nebo inspekci strojních zařízení či celých výrobních celků. Konkrétně se jedná o digitální technologii, kterou lze kompletně transportovat v příručním zavazadle. Jeho cena je asi 20 až 30 tisíc korun. Sadu tvoří holografické brýle, mikrokamera, endoskop a další vybavení. Zařízení umožňuje takzvanou virtuální teleportaci pracovníka – místo fyzického zaměstnance cestuje do vzdáleného místa pouze zmíněné zařízení, kterým je tamní operátor při určité činnosti veden. Tento systém aplikuje například Škoda Auto při složitém přestavování lisovací linky nebo společnost Škoda JS při údržbě jaderných energetických zařízení.
Výrobní závod v laboratoři
Vedoucí Katedry kybernetiky a biomedicínského inženýrství VŠB-TU Ostrava Jiří Koziorek na závěr konference představil univerzitní testbed smart factory. Tvoří jej modelové pracoviště továrny postavené na principech průmyslu 4.0. V rámci příspěvku Koziorek předvedl uspořádání a možnosti smart factory se zaměřením na aplikace využívající technologii digitálního dvojčete. Testbed smart factory umožňuje využití této technologie v průmyslové praxi a nabízí firmám, které mají zájem o rozvoj svých technologických kompetencí, spolupráci.